Description:
105 LITRE REPLACEMENT LONG RANGE FUEL TANK
NA-NG SWB | 4CYL
This tank is designed as a full replacement fuel tank with a much higher fuel payload than the standard tank. The tank takes the place of the factory fitted fuel tank, and as such are a direct bolt in solution for increasing fuel capacity.
These tanks are an engineering solution for being able to travel further with less fuel stops. They are designed to give maximum fuel capacity without affecting ground clearance and ramp over/departure angle, whilst being exceptionally strong against the most rigorous of conditions. The Brown Davis long range and auxiliary tanks allow you to get to the most remote parts of the globe where a standard tank wouldn’t take you, or as a tradesman get to that extra job site without constantly needing to stop for fuel.
Fuel Tank Construction Material
All Brown Davis long range fuel tanks are constructed from high grade 2mm 14 gauge – Aluminum coated cold rolled steel, to ensure maximum strength and durability. This gauge of steel is sufficiently resistant to damage by impact, and therefore additional tank guards are not necessary (most standard tanks are less than 2mm in material thickness). This material is specifically imported by Brown Davis based on critical specifications. Unlike aluminum, steel is not prone to fatigue from vibration and twisting as seen in off road conditions. This fatigue resistance far outweighs any weight advantage aluminum may offer. However, the aluminum coating on the specific steel used by Brown Davis, offer’s the strength of steel with the anti corrosion properties of aluminum
Key Features of a Brown Davis Replacement Fuel Tank
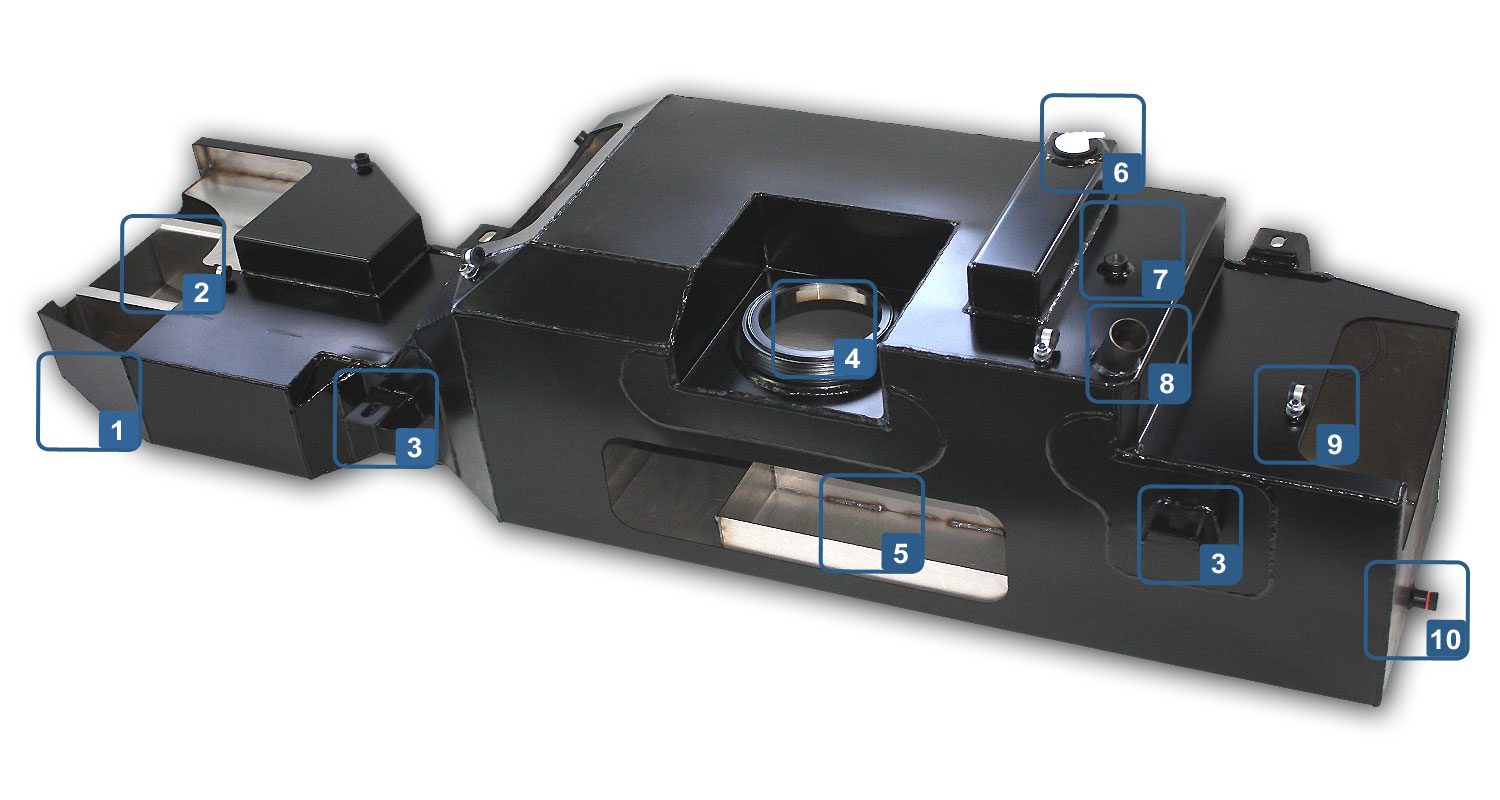
- Tapered approach angle to reduce frontal impact and improve ramp over clearance
- Longitudinal and lateral baffling system to prevent fuel slosh and to strengthen tank structure
- Gusseted brackets with double thickness pads to spread tank mounting loads
- Fuel pump sender flange designed to re-use the vehicle’s original equipment
- Swirl pot designed to carrel fuel around the pick up point
- Roll over check valve and expansion box for fuel expansion and venting
- Fast fill breather for rapid filling and to reduce bowser shut off
- Filler tube, connects to vehicles original filling point
- Cushion clamps to retain fuel lines to prevent damage and kinking
- Magnetic drain plug, horizontal and flush mounted to prevent damage
Building of a Brown Davis Fuel Tank
All Brown Davis fuel tanks go through several stages of manufacturing and quality checks to become a world leading product.
- Cutting: All tanks are laser cut to +-0.1mm tolerances to make sure all sheet metal components fit together perfectly. After cutting all sheet metal components are thoroughly cleaned for better weld quality.
- Folding: All tanks are folded using state of the art CNC machines. This allows for consistently of folds to be sure components can be assembled with minimal fuss. All tooling on the folding machinery is to precise radius to prevent weak points occurring which may result in material cracks.
- Welding of a Fuel Tank: All tanks are completely assembled before any seam welding occur. This stage of assembly we refer to as tacking. Small tack welds are used to hold sheet metal components together. During the tacking stage baffles, swirl/ fuel box and any other internal components are welded into place. After complete assembly fuel tanks are seam welded using a specialized welding gas and equipment to prevent porosity in weld. Fuel tank brackets are then welded to tank. All Brown Davis fuel tank brackets are located using a jig. Using a jig is the best way to consistently replica your vehicles mounting points for the best possible fuel tank fitment.
- Weld check: All Brown Davis fuel tanks undergo a rigorous check after they are welded. This is an inspection of the weld quality and general fuel tank presentation. It also involves a secondary check of fitting and brackets to ensure the tank has been manufactured to specification.
- Pressure Test: Another critical stage of the fuel tank manufacturing process, ensuring that each tank is perfectly sealed and leak free is paramount. As with any form of welding, there is a chance of porosity in a weld seam, which even though mostly invisible to the naked eye, can leak and pose a potential safety hazard. It is for this reason that Brown Davis incorporate several leak tests in order to ensure each tank is 100% leak free prior to leaving the Brown Davis facility. With the tank sealed and pressurized to a set level, a preliminary test is carried out as an early leak detection measure on all weld seams. This involves painting the seams with a soap based mixture which reveals bubbles at leak locations. Upon completion of this test, the tank is then fully submerged in a testing tank, and again under a set pressure level, will indicate even the most minute of air leaks via bubbles in the water
- Painting: All Brown Davis fuel tanks are painted in Satin Black to best dissipate heat. This process is mainly for aesthetic purposes as the Aluminized Steel is the best protection against external rust.
- Kit Packing: All Brown Davis fuel tank kits use the best quality products available. eg: brass hose fitting, nuts, bolts are all grade 8.8+, stainless steel hose cramp. Every kit undergoes a secondary check of components to make sure all parts required are present.
- Packaging: All Brown Davis tanks are boxed or plastic wrapped before they are dispatched. This is done in such a way to prevent damage in transit. All fuel tanks
FITTING INSTRUCTIONS
http://www.browndavis.com.au/tank-images/MPZR1.pdf
BROWN DAVIS SPECIFICATIONS | |
CAPACITY | 105 LITRE |
COMMENTS | RETAINS STD DEPARTURE ANGLE AND GROUND CLEARANCE |
FILLER POINT | STANDARD |
FITTING TIME | 2.5 hour/s |
FUEL SUPPLY METHOD | STANDARD |
MODIFICATIONS | NONE REQUIRED |
PRODUCT COLOR | BLACK |
TANK TYPE | REPLACEMENT |